Concrete structures of the Honshu-Shikoku Bridges located in straits or the nearby are in harsh environments with a large amount of salt wind from the sea. Although it is necessary to preserve the long-term durability of these structures, it is often difficult to access the structures because of their high tower piers for the sake of enabling traffic above the sea, anda large amount of cost is necessary to install scaffolding for repairs.
For the maintenance for concrete structures in these kinds of conditions, it is necessary to conduct higher precision investigations than usual and select appropriate repair methods.
Some of the concrete structures of the Honshu-Shikoku Bridges are covered with PC panels and concrete painting for the sake of aesthetics and lengthening of lifespan.
However, it is necessary to develop an economical method of lengthening the lifespan of concrete structures which are not covered with such kinds of protective measures, also, by systematically and quantitatively grasping the degree of the structures' soundness or degree of deterioration and damage and carrying out appropriate maintenance.
Therefore, currently we are taking out concrete cores, investigating the concrete's state of deterioration such as saline damage, carbonation, cracking, and corrosion of reinforcing bars, estimating deterioration and evaluating soundness based on these results in order to determine whether repair is needed.
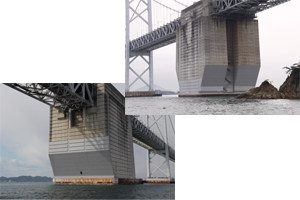
Countermeasure for salt damage by using concrete painting
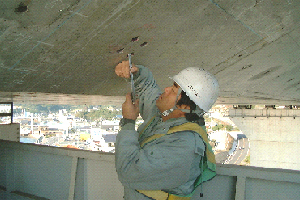
Measurement of concrete carbonation depth
For the construction of underwater substructures of the Honshu-Shikoku Bridges, a laying-down caisson method was widely used, in which a cylindrical-shaped steel structure with outer walls (called a steel caisson) is used, and after this sinks to the seabed, then concrete is poured inside it.
An investigation of the steel caisson outer wall (called skin plate) of the underwater substructure 11 years after its completion revealed that a type of corrosion called pitting corrosion is progressing locally.
As a countermeasure to this problem, we developed and adopted the electrodeposition rust-proofing method, in which by running a weak magnetic current through the seawater, positive ions in the seawater such as calcium and magnesium ions are guided to the steel caisson and coating mainly composed of calcium carbonate and magnesium hydroxide are made to adhere to the steel caisson's surface.
In areas where there is an extremely corrosive environment due to tides and sea spray, rust-proofing via painting is conducted in atmospheric environment using dry boxes.
For the Tatara Bridge and Kurushima-kaikyo Bridges, the surface of the steel caisson is painted during construction and sacrificial rust-proofing have been also conducted by attaching aluminum anodes.
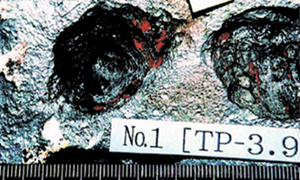
Pitting corrosion on skin plate
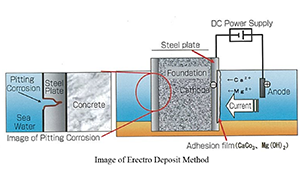
Electrodeposition rust-proofing method (Seto-Ohashi Bridge)
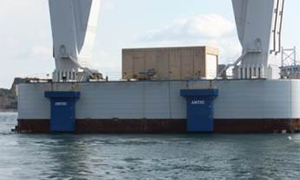
Painting of areas subject to spray and tide using dry boxes
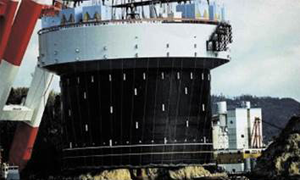
Steel caisson with aluminum anodes attached in advance
For the foundations of the towers of the Ohnaruto Bridge, located in the Naruto Strait which is famous for its whirlpools, we used a multi-pillar foundation structure in order to not disrupt the tides. The multi-pillar foundation is made up of steel pipes and internal reinforced concrete, and we carry out corrosion protection work to protect the steel pipes from corrosion.
We use different corrosion prevention methods that are appropriate for each area: underwater epoxy resin and paint are adopted for areas subjected to spray, petrolatum (a kind of petroleum wax) and a titanium cover with superior corrosion resistance are adopted in areas subject to tides, and cathodic protection is adopted in underwater areas.
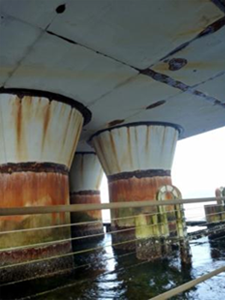
Before rust-proofing
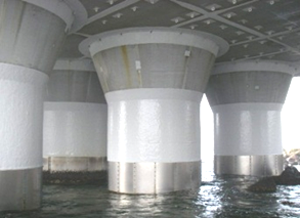
After rust-proofing